We accomplished a lot during Week 4 of CRESCENDO℠ presented by HAAS, and have exciting plans for week five.
Mechanical
This week, the mechanical subteam mainly focused on making adjustments to our initial design and testing other designs to see how they work for us. Seeing that designs with two motors, one for shooting and one for indexing, were highly effective, we modified our shooter prototype to use this style of shooting. This was especially helpful in letting the primary flywheels ramp up to speed, and only engaging them with the note when the motor had reached full power. We also swapped the flywheels for thinner, lighter ones. We plan to test this mechanism next week and either modify it or replace it entirely.
We also finalized the calculations for our lifting mechanism that uses a pneumatic system and bought the cylinders we needed. We attached the two pneumatic cylinders with hooks to a previous year's robot to see if they could lift its weight. We tested this by having two members hold a bar for the hooks to grab onto and allowing the pneumatic system to extend and retract. We were thrilled to see that the cylinders could lift it with ease, especially after one of the cylinders was slightly damaged by a fitting.
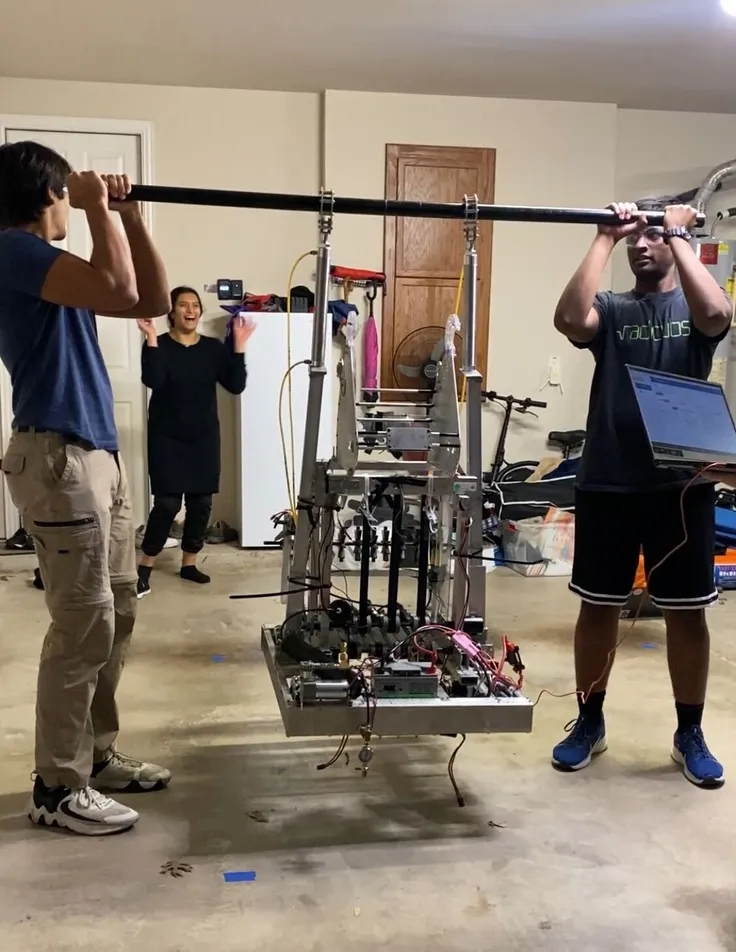
Business
This week business continued to work on drafting the Impact essay, writing the speech for the Impact presentation, and creating the business binder. We also continued to help the mech team format the engineering journal! In addition, we have finally received a pin press and will be able to print out designs to hand out at competitions.
We have also finally found and moved into our build season workspace! The space is generously being donated by the Hall Group, which is allowing us to use the space until the end of April.

Programming
This week, the programming subteam configured PhotonVision on an overclocked Raspberry Pi 4 Model B in order to detect AprilTags and calculate the robot’s relative position. This will allow us to write scripts to accurately calculate and reset the robot’s position on the field during the autonomous period, which would otherwise have to rely on the odometry alone. We may also be able to use this to quickly align to the source, amp, or speaker during Teleop, although we would have to make sure that doing so would be faster than a human driver simply aligning manually.
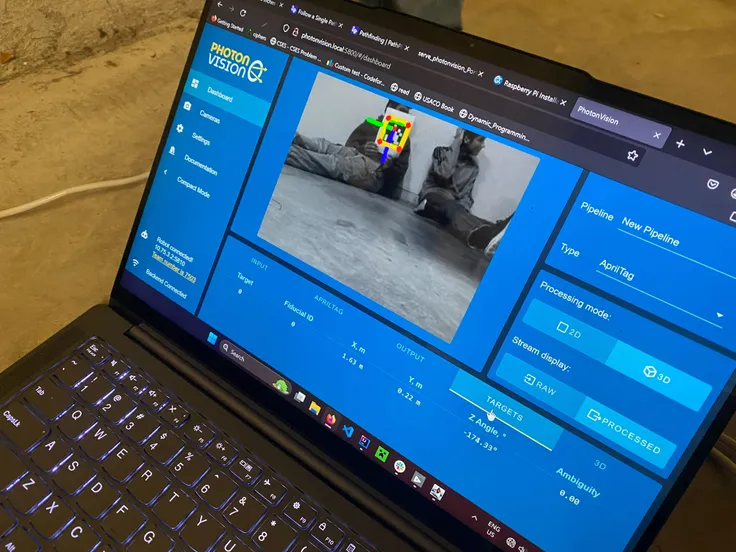